DIY Home Hardening
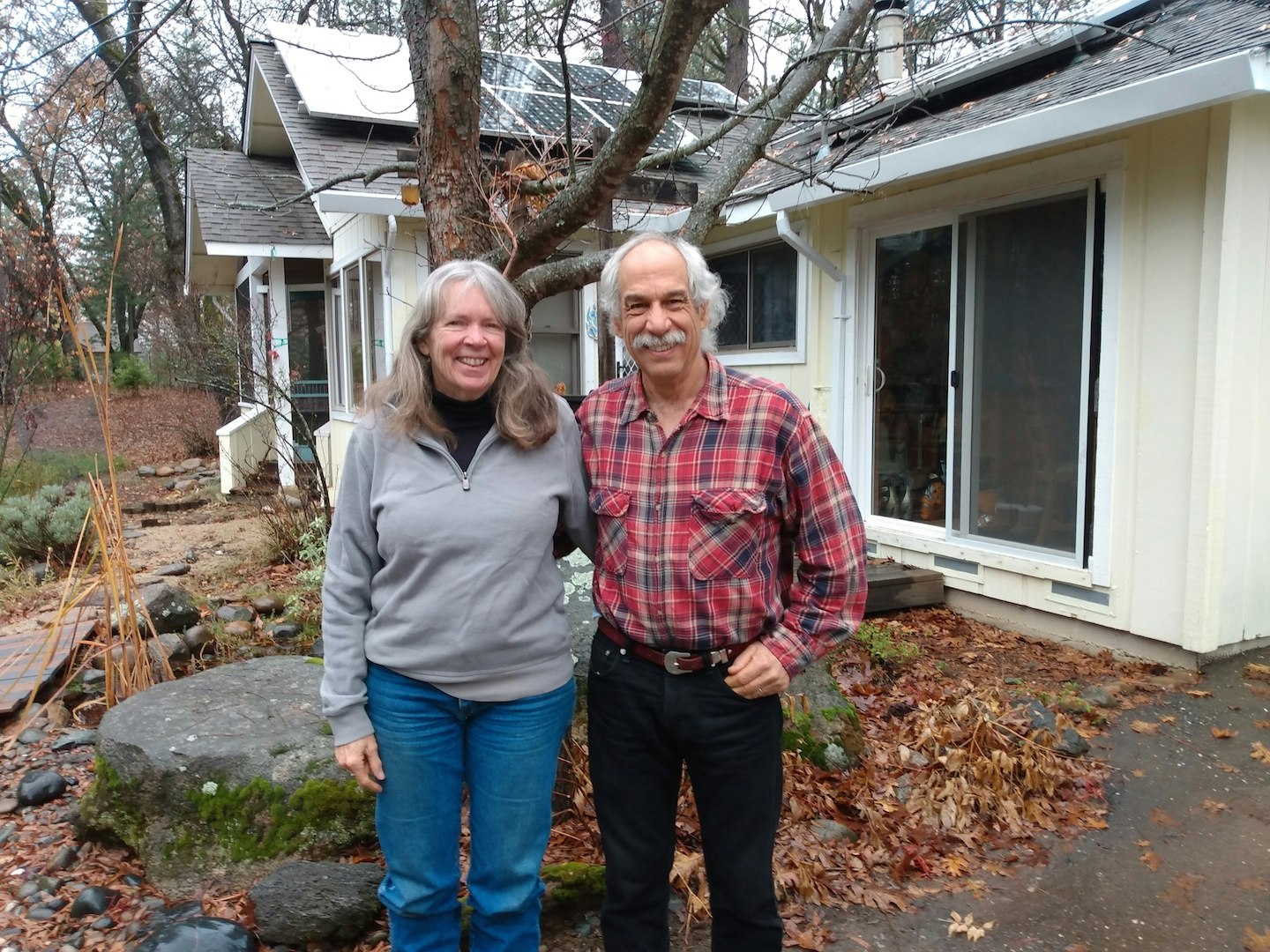
Alice and Lester recently got serious about "hardening" their 40 year old home against wildfires. They had already cleared the critical first 5 feet of all flammables, including almost all vegetation (see 11-19 story "The First 5 Feet").
Their first priority would have been their roof, but it was a newish, Class A-rated roof and did not need replacing. Whew! Next in priority were vents and gutters, shown in scientific studies to be likely access points for fire brands (embers) to ignite a home during a wildfire.
Vents
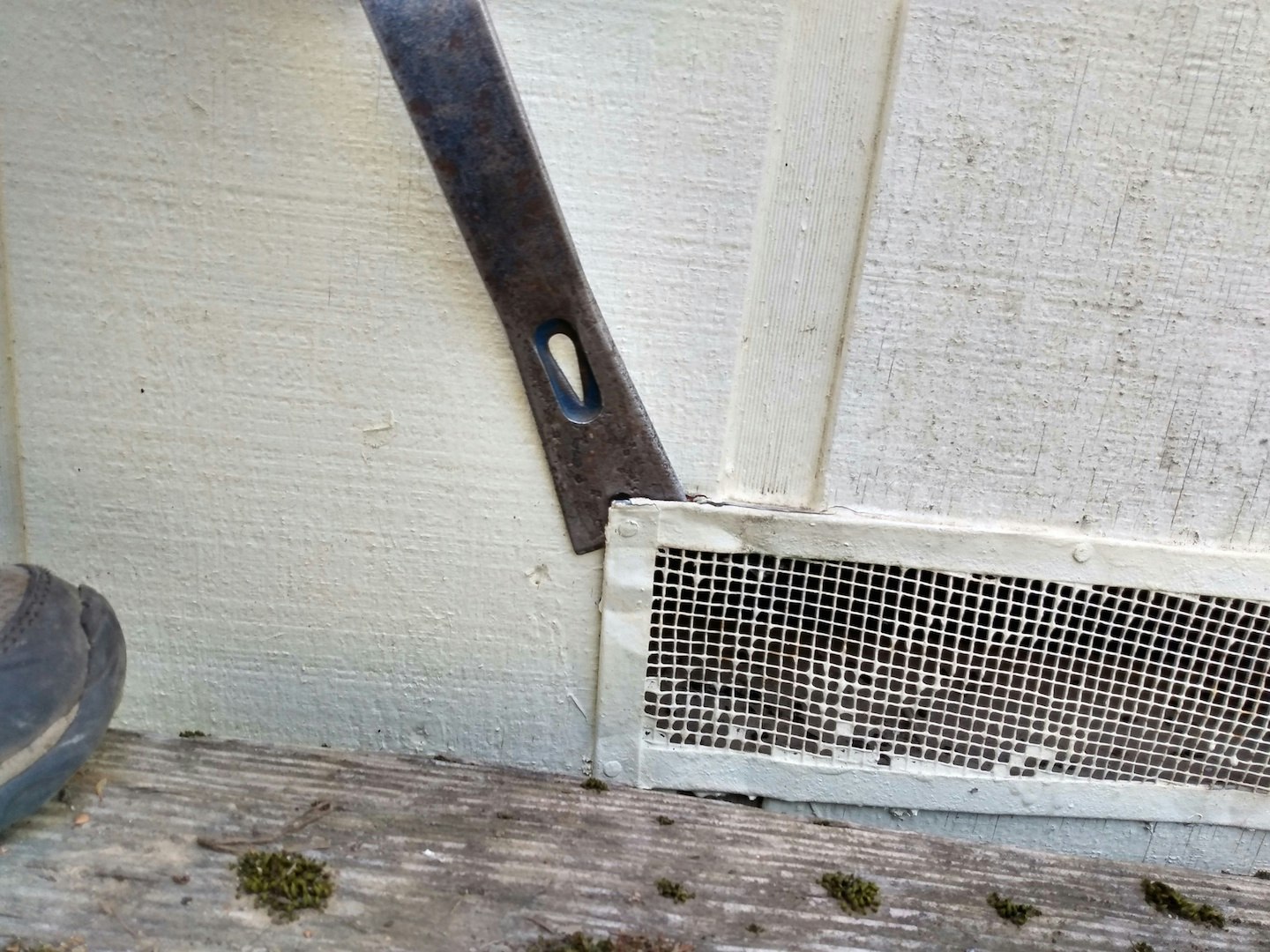
Alice and Lester could have chosen to add screens with smaller openings (1/16 inch) on top of all their vents (foundation vents at the bottom of walls, eave vents at the top of walls, and attic gable vents). Instead, they decided to spend the money and replace every vent with ones that not only had small screening but also had honeycomb openings designed to melt shut under the heat of a fire or ember.
The pair ordered new vents and material through an experienced installer, Ember Wildfire Defense Solutions out of Reno, who also supplied some welcomed advice for their DIY project. They chose one of the three brands approved for such use: the Vulcan vent. These vents, also available online, come in various shapes and sizes, as probably do the two other brands (Elite and Brandguard). A significant percentage of homes that survived the Camp Fire had such vents installed (required for new construction). Alice and Lester made this decision based on their knowledge of how often more open vents can be the ignition point for wild fires. They also had a close-to-home experience when Lester's brother lost a home in the Camp Fire.
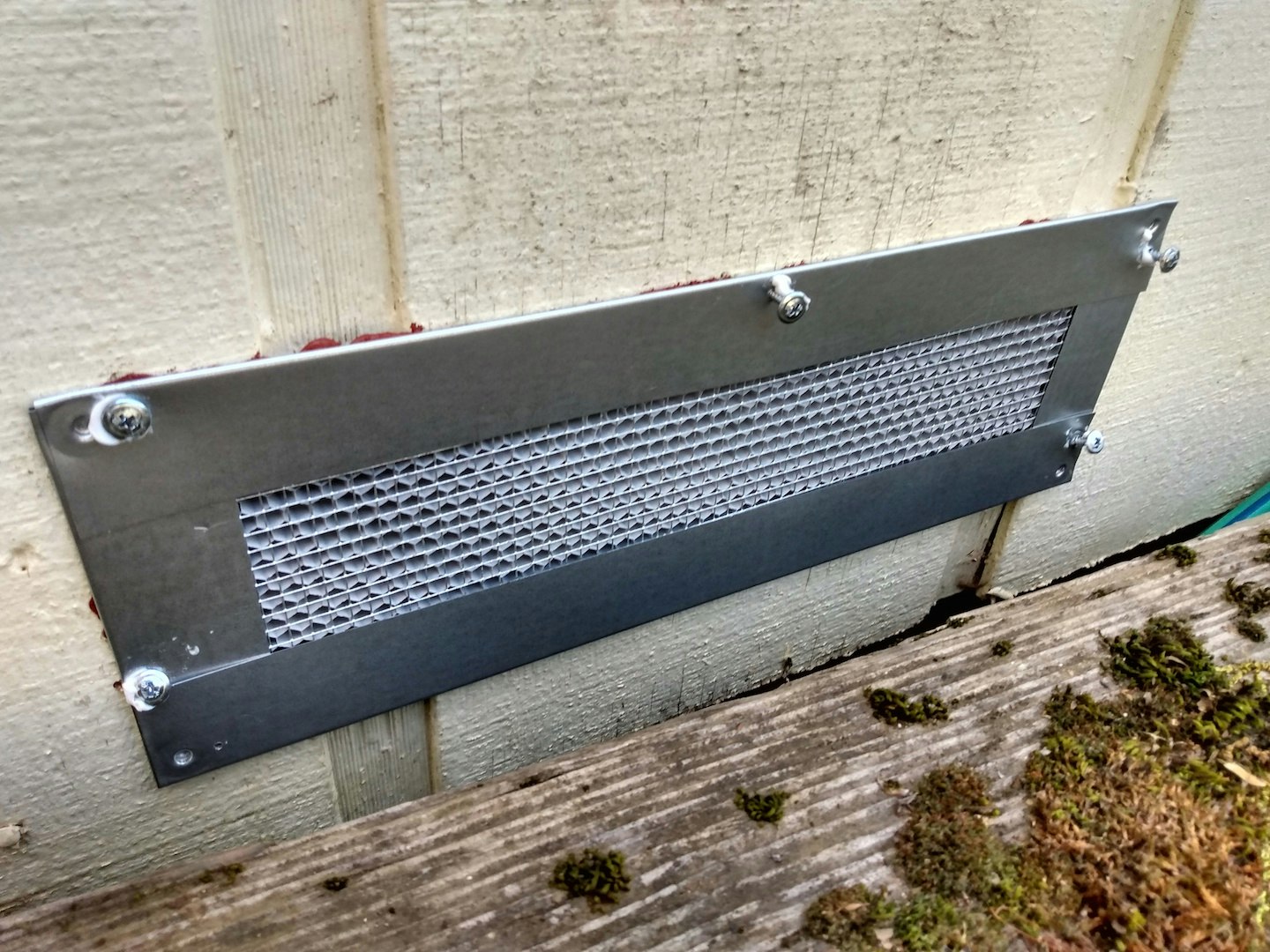
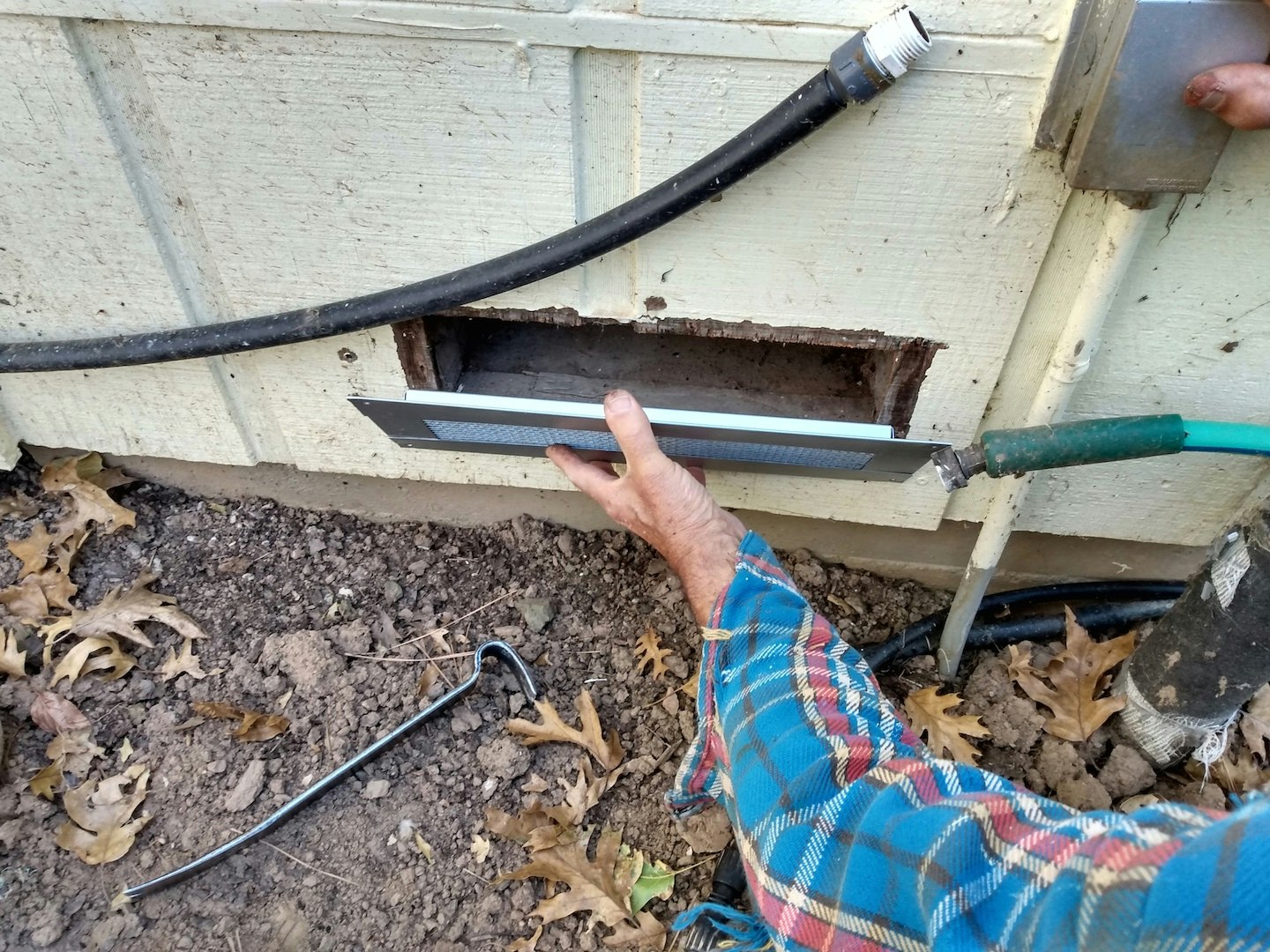
To save money, Lester chose to do the work himself. All the foundation vents and eave vents were removed from the outside and some of the openings were enlarged to fit the new vents. This was done easily with a "Multi-Max" saw Lester had on hand from a recent flooring project. That type of saw is best for this kind of cutting because it is designed to cut both wood and metal.
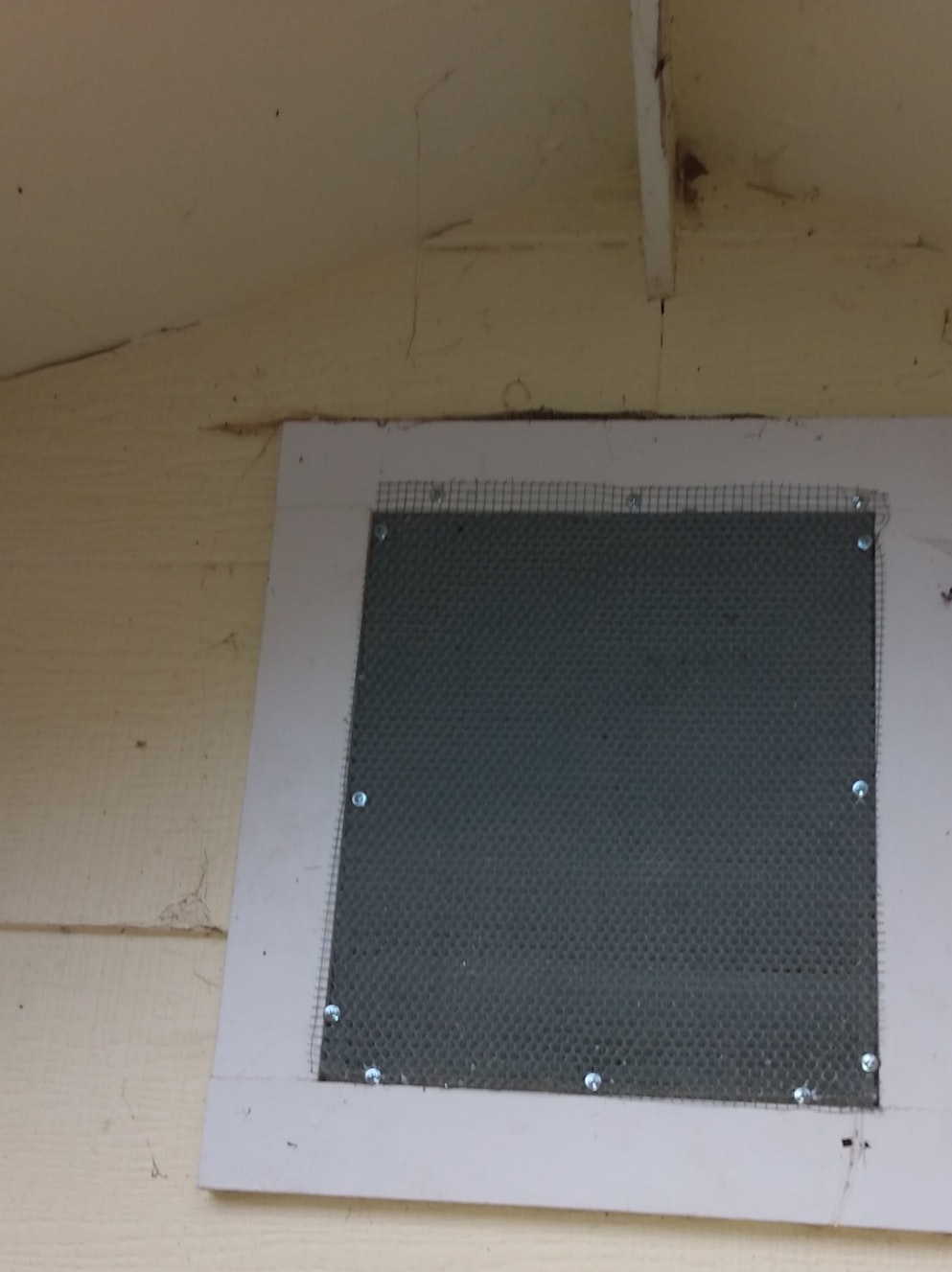
It was pretty easy to slip the new vents in from the outside, drill a few holes for screws, and attach the vents to the house. He caulked under each screw and around the upper three sides of each vent. Alice painted the vents, careful not to touch the mesh or matrix.
The gable attic vents were a little more difficult. For a few odd shaped ones (including a round one) instead of replacing the vents, they screwed a cut-to-size piece of the honeycomb meltable matrix right over the existing vents. They made a cardboard template to use in cutting the exact shape. The matrix had small, 1/16 inch metal mesh on one side, which was attached facing the inside of the attic, adding important protection to the wooden slats of the existing vents.
This process wouldn't work for two of the vents, so an entire extra vent unit was attached on top of each of those. Attic ventilation was expected to remain adequate because of the continuous ridgeline vents, .
Gutter Guards
The next priority was gutters. For a few months each Fall the pair would clean their gutters weekly to make them fire resistent. This chore wasn't particularly safe. They worried that frequent tromping around on the roof wasn't good for the roof either.
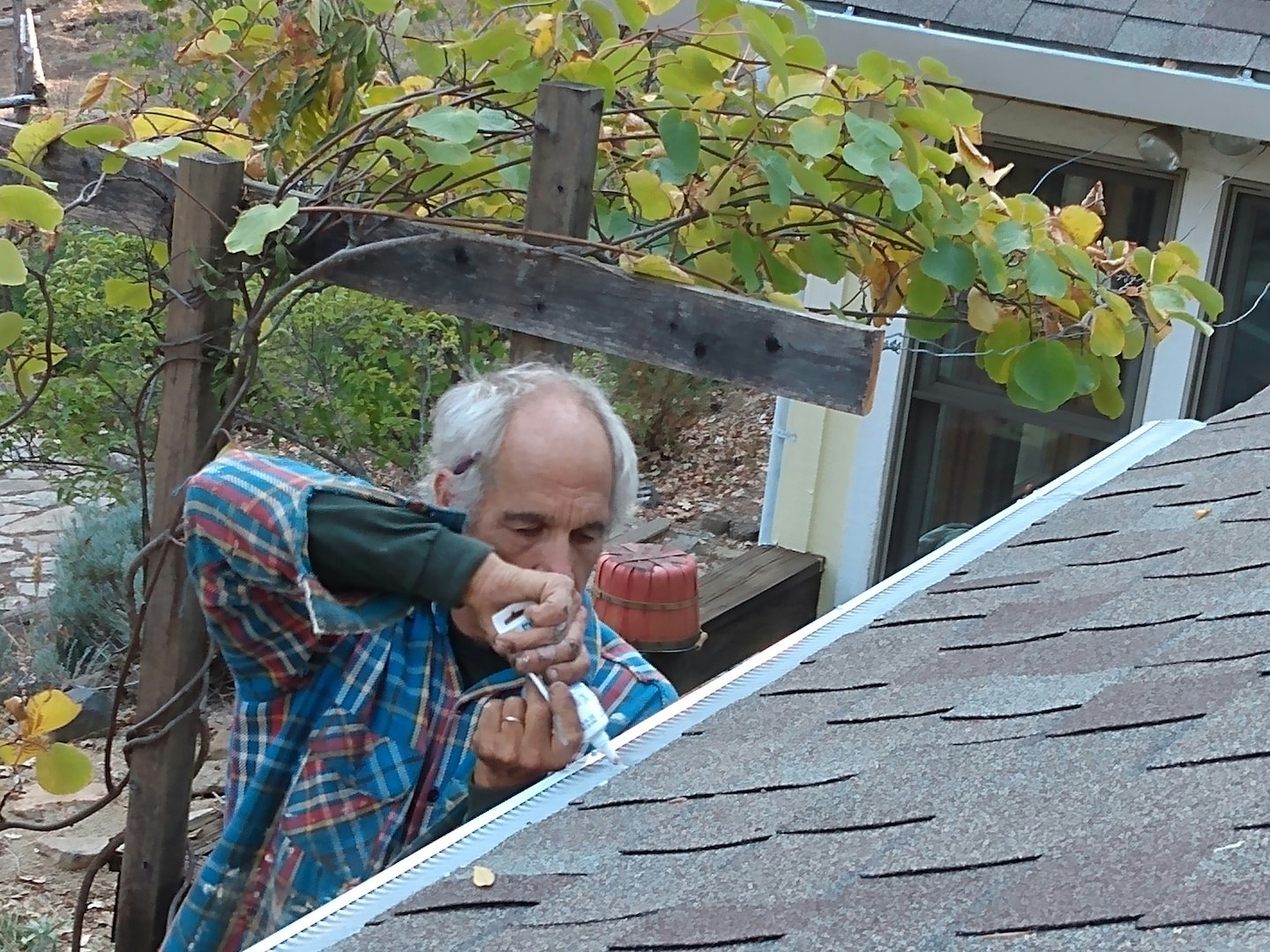
The original, cheap gutter guards were worthless and had been removed. Reviews suggested a higher quality brand with a sturdy frame and fine micromesh screening that wouldn't trap pine needles. They chose Valor gutter guards that they could install themselves. They've heard that local people who tried Leafguard found them to be successful as well.
The couple did all the measurements themselves and ordered their materials through Ember Wildfire Defense Solutions. The Reno firm gave them DIY advice for this project as well.
The project ended up being much bigger than anticipated due to the condition of the existing gutters. They were good, deep ones made of galvanized metal and painted. But they had been up for several years and needed some maintenance.
Alice and Lester sanded the rust off, repaired some pin holes, and coated the inside of all the gutters with Roof Patch to avoid future problems. They had the time and energy for this, whereas an installer may have simply replaced them with new ones. They also found some gutters needed to be rehung at a steeper angle to help the water flow.
Installing the gutter guards on top of the gutters was easy. Lester bought a carbide blade for cutting metal with his miter saw, making the few corner cuts more precise. The guards were then slipped under the roofing edge and over the roof flashing, leaving no exposed wood edge to ignite in a fire. After drilling starter holes, the pre-drilled outer edge of the guard was screwed into the lip of the gutter.
The Valor guards come in 4-foot sections which are butted together. To make the connections nice and smooth, Lester finished by caulking each butt-joint (above, right).
These sturdy micromesh gutter guards have been up over a month and are working well. The leaves tumble right over and pine needles are not getting trapped. A full year will tell if they are effective over the long term. Stay tuned!
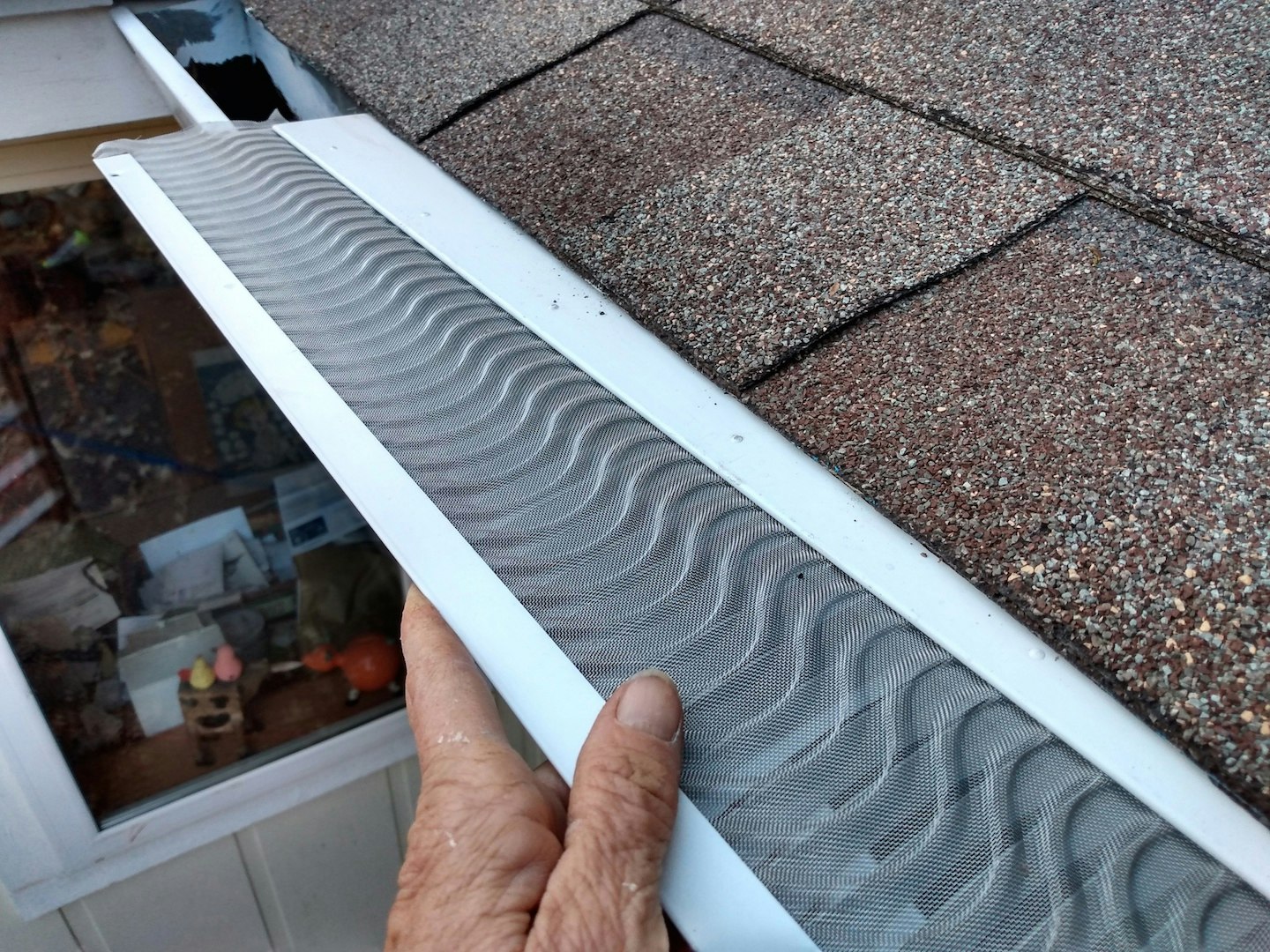
,